口罩荒?美国人在家制作N95防护罩
住在美国维吉尼亚州的杰里米,守着家里两台3D打印机24小时不间断地制作N95防护罩,希望在最短时间内送到一线。 “大家都听说了口罩严重短缺,所以我想帮他们提高口罩免受污染的可能,” 他说。 此外,杰里米坚持不收取任何费用,他认为对抗新冠病毒的医疗人员“都正面对着枪林弹雨般的威胁,他们不应该为此买单”。 杰里米和妻子艾米的这项防护罩计划在网上获得广大回响。 “最温暖的是这些反馈重新燃起我的信念,就是人们愿意共患难,这是我过去很难相信的,”杰里米说。 #新冠病毒 #N95
Original Link: VOA
Crisis Heroes: Meet the Virginia Couple 3D-Printing Mask Shields for Medical Workers
"The sooner the shields are made irrelevant, the happier I'm going to be."
WRITTEN BY DANIELLA BYCK | PUBLISHED ON
Jeremy Filko wears a 3D-printed shield over a mask. Photo courtesy of Amy and Jeremy Filko
As protective gear shortages put our frontline medical workers at risk, Vienna couple Amy and Jeremy Filko are 3D-printing shields to protect N95 masks. For each request received, the Filkos are covering shipping costs and sending four free masks to doctors, nurses, and other healthcare workers.
Three years ago, curiosity drove Jeremy, a data scientist for a federal contractor, to experiment with 3D printing, and he started making containers and tupperware. But a conversation last week with an anesthesiologist friend inspired Jeremy to turn his hobby into an aid effort.
Typically, an N95 mask is worn once and then disposed. But amid shortages, the anesthesiologist told Jeremy that medical workers are being instructed to recycle their masks for upwards of five days.
Immediately, Amy and Jeremy began brainstorming how to help. Producing the N95 masks themselves requires rigorous testing, so Jeremy opted to create a shield on his two 3D printers to protect the masks from splatter.
By Friday, he had created a prototype. Each shield is printed layer by layer and made from ABS plastic, a common type. One shield weigh seven grams and costs around 10 cents to produce.
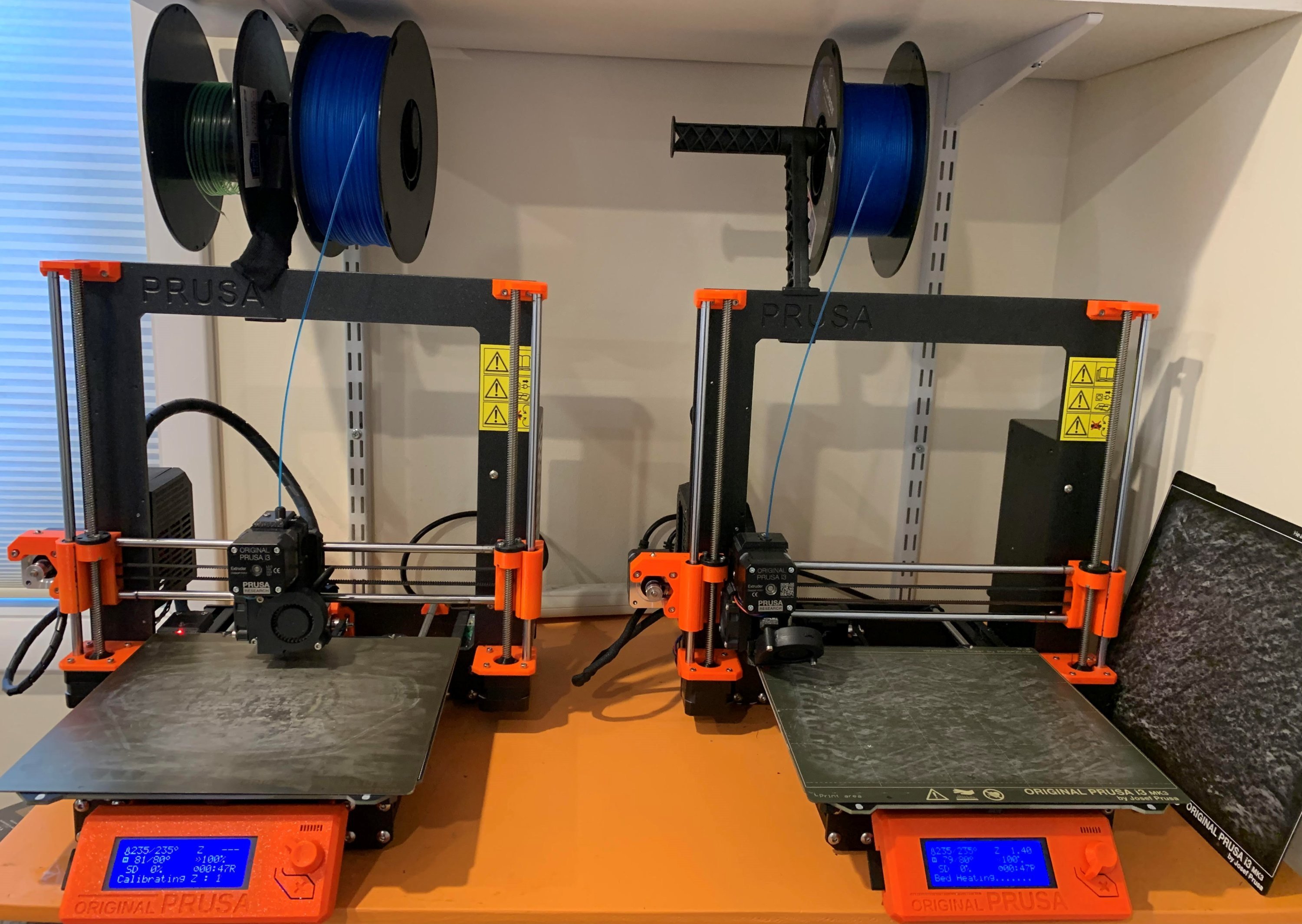
The printers are currently running 24/7, churning out a new shield every 38 minutes. To avoid losing precious production time, Amy and Jeremy are rotating shifts throughout the night to manually reload the printers.
They’ve already made around 40 shields, and the goal is to increase production numbers by sharing the file with other 3D printers. One caveat: “Anybody that we give a design to, we’re telling them do not charge. It needs to be free and given to providers free,” says Jeremy.
More printers also means more feedback for a refined design. After delivering early batches to friends in the medical field, Jeremy integrated their comments into a new design with air vents and a wider shield.
To submit a request for shields or 3D printing files, Amy, who works in communications for a federal contractor, recommends reaching out via the Facebook page she created.
“Anything that we can do to keep those masks viable longer will assist until production and distribution of the masks and filters can catch up,” says Jeremy. “The sooner the shields are made irrelevant, the happier I’m going to be.”
Original Link: https://www.washingtonian.com/2020/03/22/crisis-heroes-meet-the-virgini…